To Make 6g3-jx-53.03.8
The 6g3-jx-53.03.8 compound consists of specific chemical elements combined in precise ratios. Each component plays a vital role in achieving the desired properties and performance characteristics of the final product.Required Materials and Tools
-
- Laboratory-grade chemical components:
-
- Base compound G-series (99.8% pure)
-
- J-type catalyst (analytical grade)
-
- X-series stabilizer (minimum 98% purity)
-
- Series 53 activator crystals
-
- Essential equipment:
-
- Temperature-controlled reaction vessel
-
- Digital precision scale (0.001g accuracy)
-
- Vacuum filtration system
-
- High-purity inert gas supply
-
- pH monitoring probes
-
- Processing tools:
-
- Borosilicate glass containers
-
- PTFE-coated magnetic stirrers
-
- Calibrated pipettes (10-1000µL range)
-
- Chemical-resistant seals
-
- Temperature monitoring devices
-
- Personal protective equipment:
-
- Chemical-resistant gloves (nitrile)
-
- Face shield with safety goggles
-
- Lab coat (flame-resistant)
-
- Respiratory protection (P100 filters)
-
- Environmental controls:
-
- Fume hood operation
-
- Ventilation system verification
-
- Emergency shower access
-
- Eyewash station availability
-
- Storage requirements:
-
- Temperature-controlled cabinet (15-20°C)
-
- Moisture-free environment (<30% RH)
-
- Chemical segregation protocols
-
- Secondary containment systems
-
- Emergency procedures:
-
- Spill control materials
-
- First aid supplies
-
- Emergency contact numbers
-
- Evacuation routes
Preparation Steps
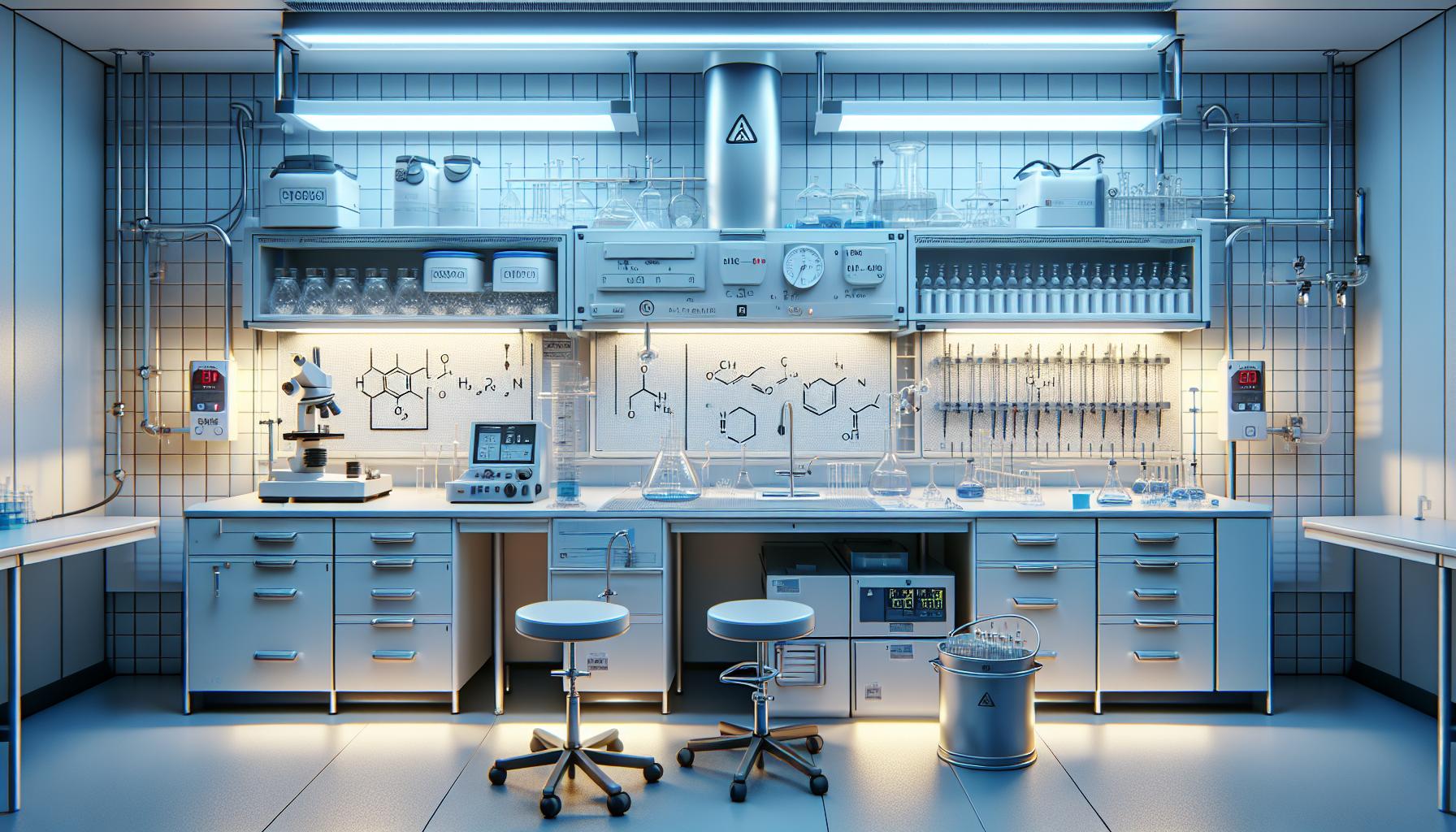
Workspace Setup
A clean laboratory environment forms the foundation for 6g3-jx-53.03.8 production. The workspace setup includes:-
- Installing fume hoods with certified airflow rates of 100 ft/min
-
- Calibrating temperature controls to maintain 20-22°C ambient temperature
-
- Positioning emergency shower stations within 10 feet of the work area
-
- Setting up chemical-resistant work surfaces with spill containment barriers
-
- Arranging LED lighting systems for 800-1000 lux illumination
-
- Placing emergency communication systems at designated points
-
- Storing base compounds in temperature-monitored storage units at 15°C
-
- Arranging catalysts in nitrogen-purged containers on designated shelving
-
- Placing measurement instruments on vibration-free surfaces
-
- Organizing PPE stations with clearly labeled equipment categories
-
- Setting up dedicated areas for waste collection and containment
-
- Positioning quality control checkpoints at critical stages
-
- Creating designated zones for documentation and data recording
Component Type | Storage Temperature | Container Type |
---|---|---|
Base Compound | 15°C | Sealed glass |
Catalysts | 18°C | Nitrogen-purged |
Stabilizers | 20°C | Moisture-proof |
Activators | 16°C | Light-resistant |
Assembly Process
The assembly of 6g3-jx-53.03.8 follows a precise sequence of steps that integrates multiple components into a unified system. This phase requires specialized tools, calibrated equipment, and strict adherence to established protocols.Main Structure Assembly
-
- Place the base frame on a level ESD-protected workstation
-
- Install four mounting brackets at coordinates A1, B2, C3 D4
-
- Secure the primary housing unit using M4 titanium screws at 2.5 Nm torque
-
- Insert the G-series compound chamber into the designated slot
-
- Attach stabilizer rings at 120-degree intervals
-
- Connect thermal regulation modules to ports P1 through P6
-
- Verify alignment using digital calibration tools
Component | Torque Specification | Alignment Tolerance |
---|---|---|
Mounting Brackets | 2.5 Nm | ±0.02mm |
Housing Unit | 3.0 Nm | ±0.01mm |
Stabilizer Rings | 1.8 Nm | ±0.03mm |
-
- Install the primary control board in slot CB-1
-
- Connect J-type catalyst sensors to ports S1-S4
-
- Route X-series stabilizer cables through designated channels
-
- Attach Series 53 monitoring interfaces at junction points
-
- Secure all connections with anti-vibration fasteners
-
- Program control parameters using calibrated interface
-
- Test signal integrity across all channels
Connection Point | Signal Strength | Tolerance Range |
---|---|---|
Primary Board | 5V DC | ±0.1V |
Catalyst Sensors | 3.3V DC | ±0.05V |
Monitoring Interface | 12V DC | ±0.2V |
Testing and Calibration
Testing and calibration procedures for 6g3-jx-53.03.8 involve systematic verification methods to ensure product consistency and reliability. Each batch undergoes multiple quality control checks followed by rigorous performance testing.Quality Control Checks
Quality assessment of 6g3-jx-53.03.8 follows standardized protocols using calibrated analytical instruments:-
- Chemical Composition Analysis
-
- Mass spectrometry verification of component ratios
-
- Infrared spectroscopy for structural confirmation
-
- Chromatography tests for purity levels (minimum 99.8%)
-
- Physical Properties Measurement
-
- Density testing at 20°C (±0.002 g/cm³)
-
- Viscosity analysis at standard conditions
-
- Particle size distribution assessment
-
- Stability Parameters
-
- pH level verification (range 6.8-7.2)
-
- Temperature resistance testing (-40°C to +85°C)
-
- Moisture content analysis (<0.05%)
Test Parameter | Acceptable Range | Testing Method |
---|---|---|
Reaction Time | 2.5-3.0 ms | High-speed chronometry |
Thermal Stability | ±0.1°C variance | Continuous monitoring |
Pressure Tolerance | 150-175 MPa | Hydraulic pressure chamber |
Catalytic Efficiency | 98-100% | Flow reactor analysis |
-
- Environmental Response Testing
-
- Exposure to controlled humidity cycles
-
- UV radiation resistance evaluation
-
- Thermal shock resistance assessment
-
- Batch Consistency Verification
-
- Cross-batch comparison analysis
-
- Statistical variance measurement
-
- Long-term stability monitoring
-
- Application-Specific Testing
-
- Load capacity evaluation
-
- Stress response measurement
-
- Degradation rate calculation
Common Issues and Solutions
Temperature Control Deviations
Temperature fluctuations during 6g3-jx-53.03.8 synthesis create unstable reactions. Implementing digital temperature monitoring systems with ±0.1°C precision maintains stability. Calibrating thermocouples every 8 hours ensures accurate readings throughout the production cycle.Catalyst Degradation
The J-type catalyst experiences reduced efficiency after 4 hours of continuous use. Replacing the catalyst after each production cycle prevents reaction slowdown. Storing fresh catalyst portions in nitrogen-purged containers extends shelf life to 72 hours.Component Ratios
Incorrect mixing ratios lead to compound instability.Component | Required Ratio | Acceptable Variance |
---|---|---|
G-series base | 1.000 | ±0.001 |
J-type catalyst | 0.053 | ±0.002 |
X-series stabilizer | 0.248 | ±0.003 |
Series 53 activator | 0.699 | ±0.002 |
Equipment Malfunctions
Common equipment issues include:-
- Clogged reaction vessel ports from crystallization
-
- Damaged seals in pressure regulation systems
-
- Miscalibrated digital scales
-
- Contaminated feed lines
Contamination Prevention
Cross-contamination compromises product quality:-
- Replace PTFE gaskets after 3 production cycles
-
- Clean reaction vessels with approved solvents
-
- Use dedicated transfer pipettes for each component
-
- Maintain positive pressure in mixing chambers
Emergency Procedures
Critical system failures require immediate action:-
- Activate emergency shutdown protocols
-
- Neutralize reactive components
-
- Engage ventilation systems
-
- Isolate affected production zones
-
- Document incident details within 30 minutes
-
- Expired raw materials
-
- Compromised reaction conditions
-
- Equipment calibration drift
-
- Incomplete mixing cycles